

Here Is Everything You Need To Know About Single Wires And Stranded Wires
Wires play a pivotal role in electrical applications. Two types of wires find frequent use for domestic and commercial purposes–solid and stranded wire. Solid wires have a solid core, whereas stranded wires have several thinner wires warped in a bundle shape. Each wire has its distinct advantages. The wire usage depends on the specific project details.
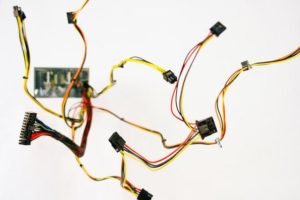
Several factors govern the eventual choice between single and stranded wires. The metal type for use, amperage load and application, wire gauge, and costs are deciding factors when choosing the correct wire. Knowing the strengths and weaknesses of the two-wire types will make it easier for you to make the best choice for your individual needs. Here are some criteria you should know in the wire selection process.
Introduction To Single Vs. Stranded Wire

A single or solid-core wire is, by its very name, one piece of metal wire. It is suitable for all-weather and can withstand movement. Single wires are ideal for heavy-duty outdoor applications that involve higher currents and rigid durability. Infrastructure building and vehicle controls are areas where single wires find the best use. Such wires are anti-corrosive and low-cost.
Thin, bundled wires make a Stranded Wire. The stranded wires are easy to twist and bend to fit knotty spaces. A stranded wire is more flexible than a solid wire and barely splits. It finds optimum use in indoor applications like circuit boards, speaker wires, and electronic devices where twisting and bending are essential to connect electronic parts. A car door is an ideal application of stranded wire where frequent bending happens.
Exploring The Wire Differences

While comparing the solid and stranded wires, you will get a better picture of the benefits and disadvantages. It also helps you narrow down the choices based on your project requirements, specific wire characteristics, and expected use. First, you must know the wire type relevance and compliance with weather changes and splitting resistance. Then, select the wire that meets your needs. Here are the key differences between a solid and multi-stranded wire to make a note of:
Current Capacity: The single wire is thicker. This gives it less dissipation area. The stranded wire has thinner wires containing air gaps. Each stranded wire offers a greater surface area and, therefore, more dissipation. The solid wire is a workable option for house wiring as it brings higher current capacity than a stranded wire.
Routing: Stranded Wire is more flexible than solid wire owing to its superior bendable quality. This makes it easier to route around obstacles than single solid wires.
Flexibility: Stranded wires give you more stretching properties because of their flexible properties. Solid wires, on the contrary, may need frequent replacement in electrical applications that require substantial movement or vibrations. Most industrial wires have multiple wire strands rather than a solid wire, allowing them to bend and flex more easily.
Manufacturing: Solid wire making involves a single wire production. Hence, it is simpler to manufacture. Stranded wires involve complex manufacturing to twist the independent wires together.
Cost: A Multi- Stranded Wire has complex manufacturing processes. A solid wire has lower production costs; hence, more affordable than a stranded wire.
Distance; Solid wires are better for longer distances as they involve less current dissipation. Stranded wires, meanwhile, perform well over concise distances.
There is no clear choice between a single vs. stranded wire, as each option poses distinctive advantages in specific situations. You need to use your discretion when opting for single and stranded wires.
Stranding Arrangements For Multi-Stranded Wiring
There are several geometric arrangements for business projects involving multi-conductor wiring. Following are the geometries for consideration in the wire and cable manufacturing process:

Concentric Display: In this typical wire arrangement, the conductors are circularly arranged. The prime benefit of this arrangement is that the wires are tightly bunched together to maintain the wire’s shape. This reduces the need for extra filler material.
Rope Display: This arrangement clusters independent strands in numerous small bundles. The bundles are then arranged concentrically to help increase the final wire flexibility. Rope arrangement is ideal for electronic applications involving a large wire size, depicting the product’s sturdiness and serviceability.
Bunch Display: In a bunch arrangement, the wires are not organized in a specific geometry but grouped together and then twisted to keep them tightly packed.
Annual Arrangement: The conductors are concentrated around a circular core in a non-conductive way in this arrangement. This enables the conductor material to keep its shape and helps reduce the wire’s resistance power.
The Bottom Line
Choosing the most effective type of wire is key to its efficiency. It also helps reduce the odds that your electrical project may need ahead of the completion stage. Consider the wiring variables of your project. Work with your manufacturing team’s designers and engineers to ensure optimum wiring choices. Remember, if a wire in your product cannot withstand cracks, it is not likely to be well-received by traders and customers. Electricians must choose the appropriate wire gauge based on the amperage load and project application.